PROCESSES
ISOTROPIC SUPERFINISHING
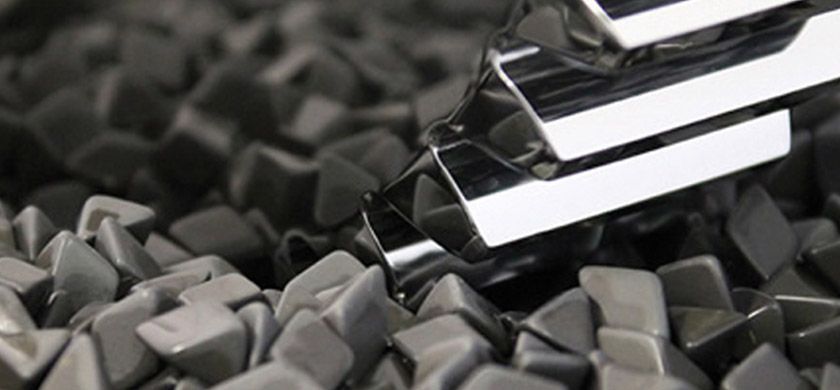
ISF® e REM®
The Isotropic Superfinish process (or simply ISF®) is used on those components that require enhanced performance and output. The process gives the component an isotropic finish, that is, a non-directional, uniform surface finish with a low Ra obtained by lowering the roughness and increasing the compressions so as to enhance the performance of these components. The process is achieved with the use of high density vibratory finishing media and chemical accelerants selected based on the user’s requirements. We use twin-bowl vibratory finishing machines for components that can be processed in large batches, as well as vibratory machines for a single piece which can be secured. (mv vibratory machine)
SUITABLE COMPONENTS FOR THIS TREATMENT:
Gears, motor shafts, turbine vanes, impellers for compressors, power transmissions, blades for aeronautics, toothed joints, punches for dies, aerospace turbine blades. Industries: Energy, automotive, motorsports, aerospace, military, earthmoving machinery, hydraulics, pneumatics, etc.
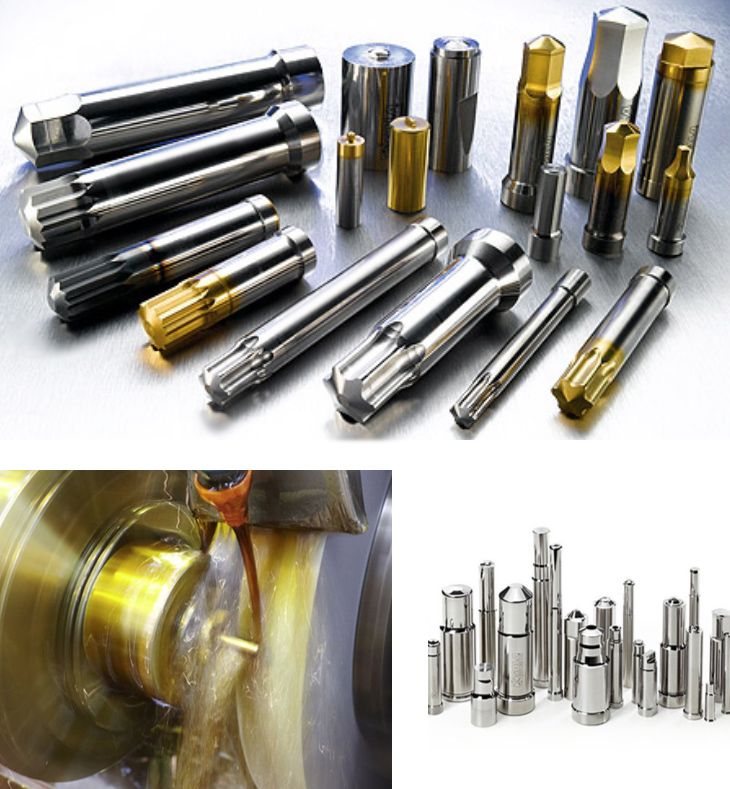
BENEFITS
2. No surface stress or tension resulting from upstream processes.
3. No pitting on gear surface.
4. Increased surface microhardness.
5. Improved fatigue strength.
6. Dimensional integrity remains intact.
7. Improved lubrication.
8. Extended life of the part.
9. Longer times between maintenance.
10. Lower operating costs.